Safe, reliable and economical the Sundyne API 610, OH6, Integrally geared pump
Sundyne API 610, 11th Edition OH6 Integrally Gear Driven Pumps are engineered for critical high-head, low-flow, heavy-duty services required by process and rotating equipment engineers within the hydrocarbon, chemical, petrochemical, power generation, gas production, and specialty processing industries. Sundyne pumps are renowned for high suction pressure and a wide range of operating temperatures.
Unlike conventional multi-stage pumps, Sundyne computer tailored hydraulics place the B.E.P. (best efficiency point) at the rated point resulting in optimum efficiency. An added benefit is reduced end-of-curve horsepower, allowing for smaller driver sizes resulting in energy savings.
Flows to 400 gpm (73 m³/hr)
Heads to 6,300 ft (1,348 m)
Suction Pressure 1,800 psi (126 kg/cm²)
Temperature Range -200 to 650°F (-130 to 340°C)
Multi-stage performance in a single stage pump
The vertical configuration of the integrally geared line of Sundyne pumps is specifically designed to save valuable space in refineries, NGL production, petrochemical and chemical plants.
APPLICATIONS
Feed pumps
Booster pumps
Bottoms pumps
Wash water pumps
Reflux pumps
Condensate pumps
Proven to be reliable, safe, compact and efficient, Sundyne LMV 346 OH6 integrally geared pumps provide a number of operational benefits:
Single stage, vertical in-line overhung pump according to ISO 13709/API 610 OH6 design recommendations for integrally geared pumps
Maximized up time
Saves space-25% the size of competing horizontal pumps
ATEX certified
Continuous operations for 5 years with no overhaul
Barske impeller low NPSH technology
Optimized pump engineering to meet the BEP – Best Efficiency Point to save energy through efficiency
US 60 Hz
- Heads to 6,300 ft
- Flows to 400 gpm
- Standards API 610 OH6
- Maximum Motor Power 400 HP
- Temperature Range -200 to 650°F
- Maximum Case Working Pressure 3,469 psi
- Maximum Suction Pressure 1,800 psi
- Differential Head 6,300 ft
- Maximum Viscosity 750 cp
- Solids Range 0.015″, 400 microns
- Mounting Configuration Vertical
- Seal Configurations Single, Double, Tandem
- Available Inducer Yes
- Available Flanges 600#, 900#, 1500# ANSI RF & RTJ
- Suction and Discharge Size 3″ x 2″
- API Plans 11, 12, 13, 21, 23, 31, 32, 41, 52, 53, 54, 61, 62, J
Metric 50 Hz
- Heads to 1,348 m
- Flows to 73 m3/hr
- Standards API 610
- Maximum Motor Power 315 kW
- Temperature Range -130 to 340°C
- Maximum Case Working Pressure 244 kg/cm2
- Maximum Suction Pressure 126 kg/cm²
- Differential Head 1,921 m
- Maximum Viscosity 750 cp
- Solids Range 0.381mm, 400 microns
- Mounting Configuration Vertical
- Seal Configurations Single, Double, Tandem
- Available Inducer Yes
- Available Flanges 600#, 900#, 1500# ANSI RF & RTJ
- Suction and Discharge Size 3″ x 2″
- API Plans 11, 12, 13, 21, 23, 31, 32, 41, 52, 53, 54, 61, 62, J
LMV 346 BUILD CODES | A | E | J | O (1) |
API 610 BUILD (2) | S-5 (3) | A-7 (4) | S-8 (4) | N/A |
Pump Case | C.S. | 316 SS | C.S. | 316 SS |
Case Studs | B-7 | B-7 | B-7 | B-8M |
Seal Housing | C.S. | 316 SS | ||
Separator | 316 SS | 316 SS | 316 SS | 316 SS |
Diffuser Insert | C.S. | 316 SS | ||
Diffuser Cover | C.S. | 316 SS | 316 SS | 316 SS |
Impeller | 316 SS | 316 SS | 316 SS | 316 SS |
Impeller Bolt | 316 SS | 316 SS | 316 SS | 316 SS |
Inducer | 316 SS | 316 SS | 316 SS | 316 SS |
Tab Washer | 316 SS | |||
Shaft Sleeve | 316 SS | 316 SS | 316 SS | 17-4 PH |
Throttle Bushing | 316 SS | 316 SS | 316 SS | |
Metal Seal Parts | 316 SS | 316 SS | 316 SS | 316 SS |
Stationary Face | Binderless Carbon or Silicon Carbide | |||
Rotating Face | Tungsten Carbide with Cobalt or Nickel Binder | |||
Shaft (all) | 4140 Steel to 0° F, 15-5PH from 0° F to –240° F | |||
O-rings | As Required |
- “O” build temperature range 0° to –240° F. Pressure capability is reduced due to strain hardened pump case studs. Contact Application Engineering.
- See Sundyne Corporation exceptions/clarifications to API 610, 11th edition for material requirements of pump parts.
- Impeller is upgraded to 316SS. A seal gland is not required because the seals mount in the seal housing. O-Rings are used instead of a case gasket.
- A seal gland is not required because the seals mount in the seal housing. The pump shaft is AISI 4140 because it is not exposed to the fluid. O-Rings are used instead of a case gasket.
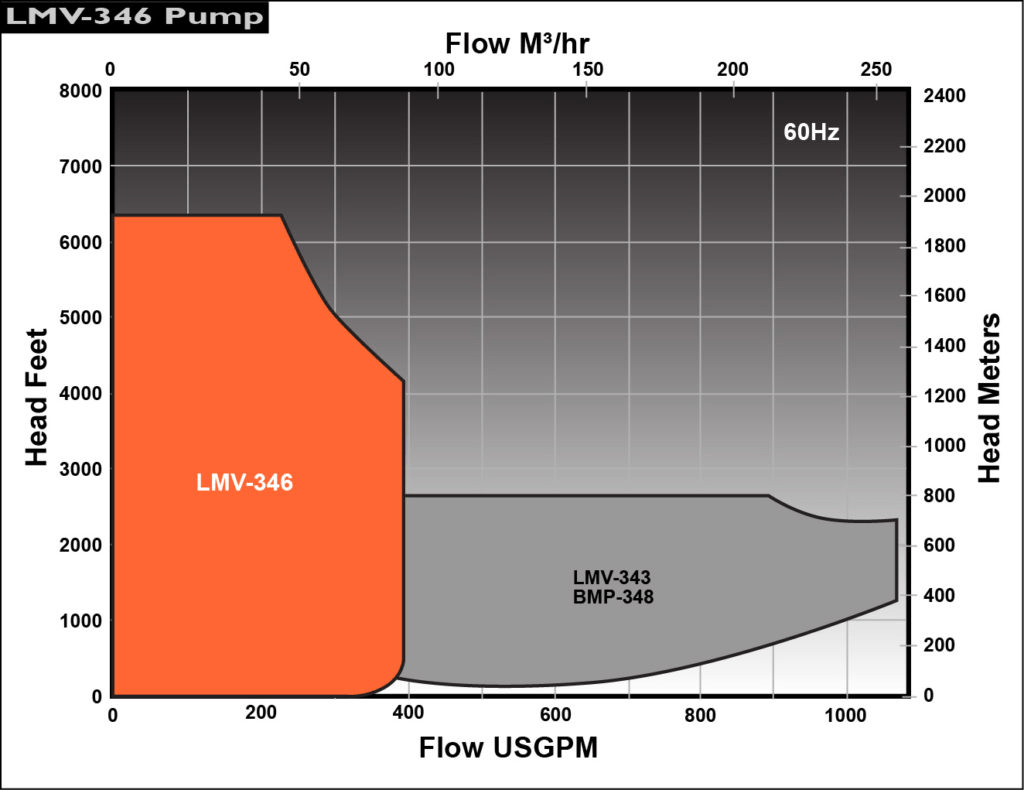
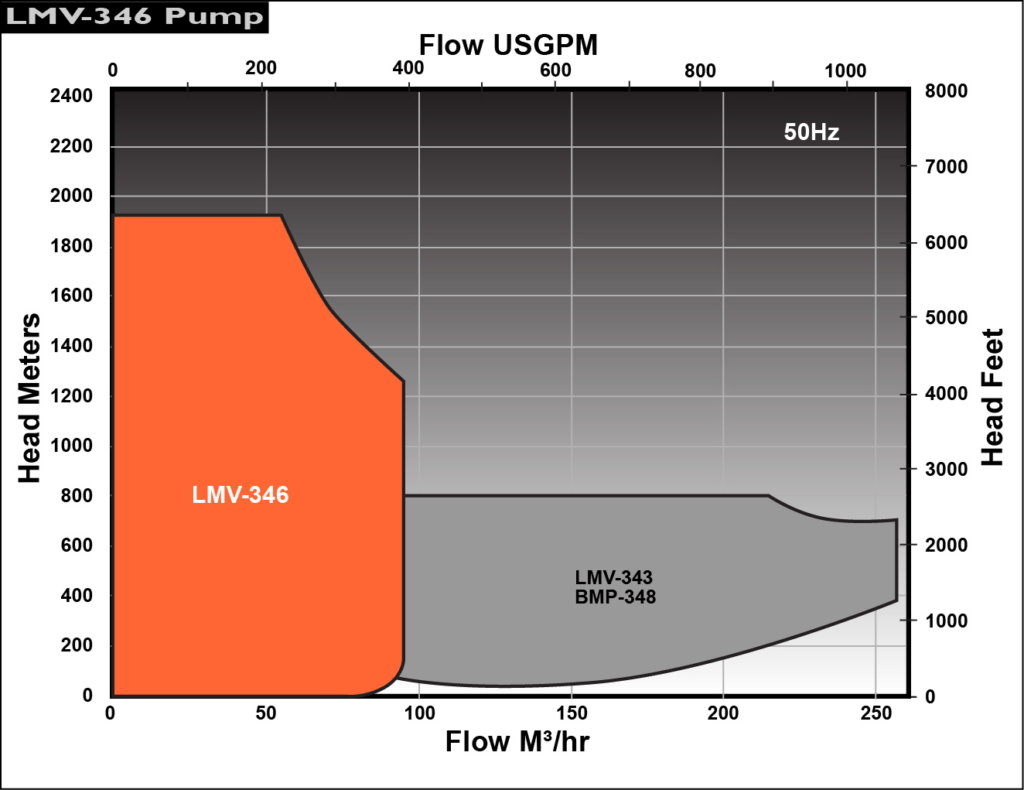
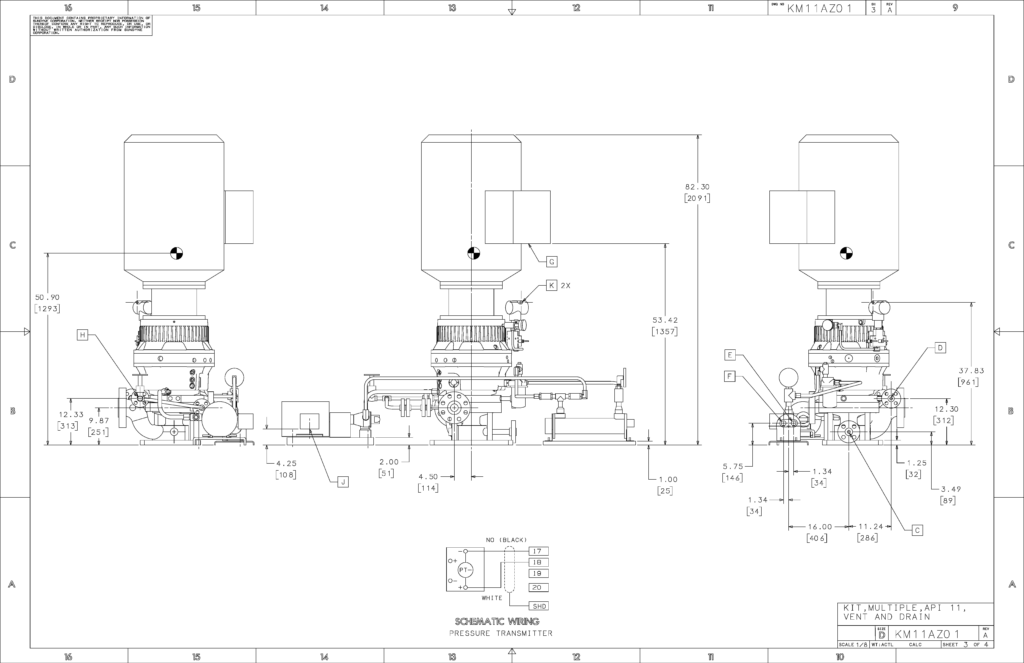